Fore!
I am often asked to check or to diagnose faults after another workshop has diagnosed the vehicle. This is sometimes at the request of the vehicle owner or the workshop.
A second opinion is sometimes sort if the repairs are costly bizarre or if the workshop can't make head nor tail of the data presented.
This Golf had a running fault which was diagnosed as the Air Mass Meter. A new unit was fitted the codes cleared and the vehicle given back to the owner.
The malfunction indicator lamp or MIL was no longer illuminated, however the car felt flat and was using an alarming amount of petrol.
The EPC warning light would illuminate above 4000rpm and extinguish once the rev's dropped.
The garage agreed to look at the car for no extra charge but could not determine what was wrong, the fault code or DTC was for a short to positive at the air mass meter. They could find no such fault.
I was asked to look at the vehicle, I took it for a test drive observing data driving style and the performance or lack of it.
Using the VCDS software on the laptop I was able to retrieve all the fault codes stored.
P1145 Mass Air Flow Sensor Short to Positive
P1141 Load calculation cross check : implausible value
The next step is to establish what is the data telling us, using the graphing function of the VCDS software.
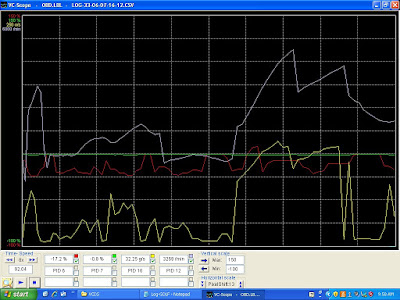
The air mass output (yellow trace) looks to mirror the engine speed (white Trace). The short term fuel trim (red trace) is negative during most of the data shown. the Long term fuel trim (green trace) is not showing much as the codes have just been cleared. This re-sets the long term fuel trim. I use this technique as the short term trim is for a short period of time is now reporting total fuelling adjustment.
From this we can establish that the engine is receiving too much fuel. This now makes sense, the P1141 code suggests that the load calculation does not agree with the data stored in the PCM look up tables.
How is load calculated? It depends on the system fitted to the vehicle, but typically it is the Throttle position, Manifold vacuum, engine speed, and air mass sensors that are used.
So the two codes are linked by the air mass, but it is a new unit. It couldn't be faulty could it?
By scoping the sensor we can eliminate the short to ground, the output looked good, no shorting out but the EPC light still illuminates.
I checked with the the vehicle owner and a non OE air mass has been fitted. There are two different types for this variant of the Golf, does the local motor know this?
A new air mass sensor from Volkswagen was ordered, fitted and after a successful test drive the codes cleared and the vehicle returned to the owner.
So the warning here is modern engine management systems require precise inputs from the various sensors a variation as small as 0.2V will cause running problems, fault codes and legislative failures.